In today’s rapidly evolving landscape of modern manufacturing, embracing digital transformation (DX) is essential to remain competitive. 92% of global manufacturers have started their DX journey, modernising traditional processes with innovative solutions.
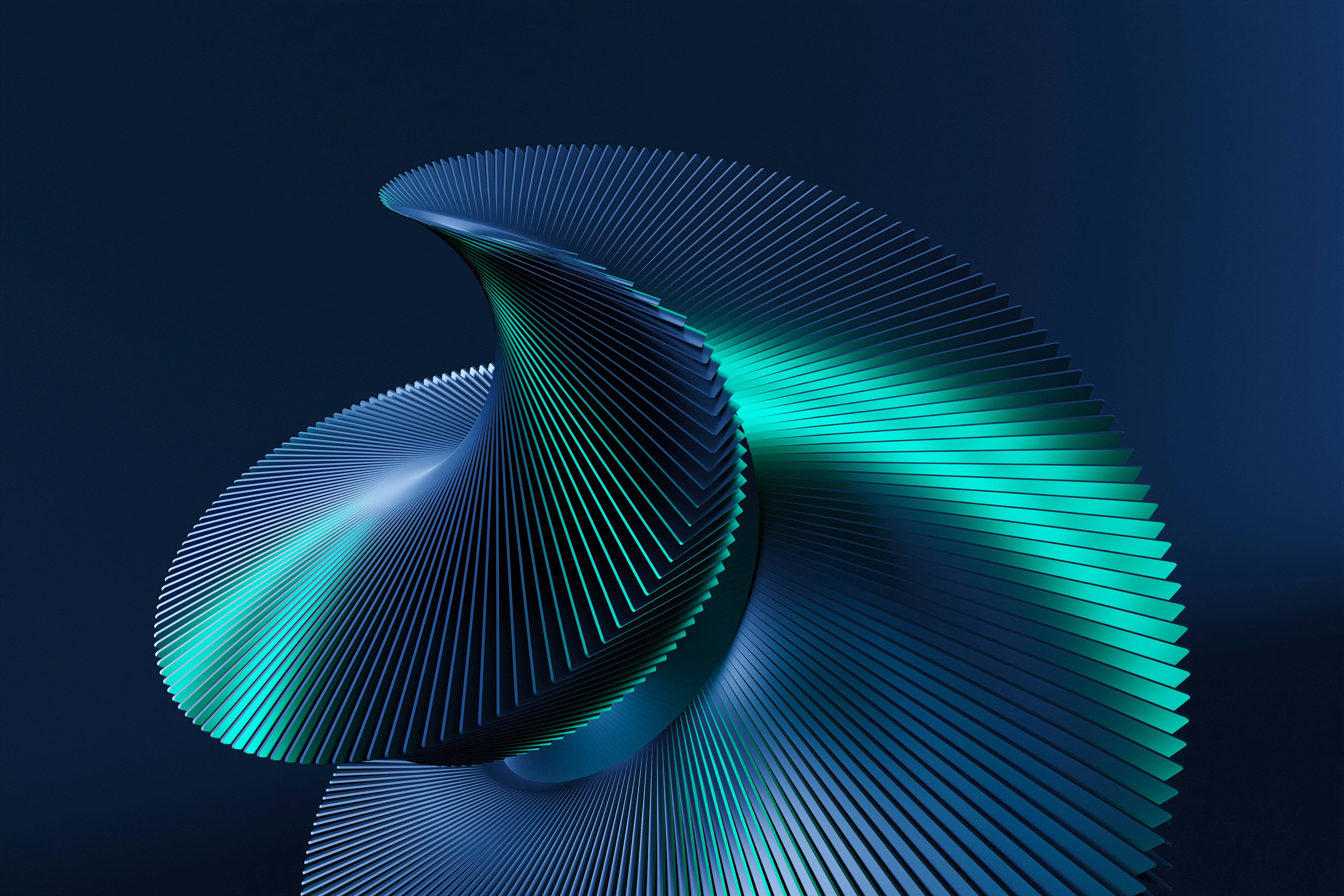
DX is revolutionising all aspects of manufacturing, from equipment monitoring to the automation and management of workflows. With proper planning and preparation, companies can effectively prepare teams and workplaces for a seamless transition to DX, unlocking new levels of operational excellence.
Manufacturing businesses must evaluate relevant use cases before implementing new technology. These include smart manufacturing initiatives including automated processes, asset monitoring and augmented processes.
1. Asset monitoring and utilisation
By implementing asset monitoring measures, manufacturers can address common challenges and gain visibility into operations, disparate equipment, product lines and production processes. This enhanced shop floor visibility increases throughput and improves energy consumption management. This helps manufacturers stay aligned with overall productivity gains.
The continuous tracking of manufacturing equipment and machinery performance is crucial to gaining oversight of operations. IoT is involved in this step, with sensors collecting real-time data on operational statuses and efficiency. Advanced insights identify any hazardous conditions or malfunctions in equipment that can lead to risks.
Asset monitoring gives companies detailed insights into equipment performance, status, condition, availability and overall utilisation. Data-driven decisions can then be made, leading to optimal productivity.
2. Predictive maintenance
Unexpected faults in equipment can be highly costly and disrupt production workflows. Predictive maintenance is an emerging goal for manufacturers to boost service productivity by identifying signs of malfunction early. Smart technology such as IoT sensors are utilised to monitor equipment data such as temperature, vibration and asset failures to predict when faults may occur.
This modern technology assesses the severity and location of potential failures to catch issues before they escalate into larger problems. This saves manufacturing companies significant costs as issues can be solved before product downtime occurs. These product insights enhance efficiency for service and maintenance teams as they can pinpoint specific issues.
Investing in predictive maintenance is worthwhile for many companies as machine learning goes beyond the capabilities of manual efforts. Regularly maintained equipment operates more reliably, extending product lifespan.
3. Augmented processes
Introducing advanced technology creates the need for improved training workflows. In particular, digital work instructions simplify training for both current and prospective employees.
The more efficiently manufacturers provide less experienced workers with the right information at the right time, the more productive the workforce becomes. Implementing augmented processes streamlines knowledge flow from experienced workers to the rest of the team. This way, product updates and information on changing processes can be easily communicated to the workforce. Digital work instructions can be updated more efficiently than print materials which take more time to revise.
Companies that leverage digital augmented processes will have more success in upskilling and onboarding employees.
4. Digital performance management
Conventional manufacturing performance systems are often outdated, relying on analog and isolated systems to oversee operational performance. This results in miscommunication gaps during data gathering, leading to delays and product downtime.
By adopting digital performance management systems, these traditional methods are integrated with modern systems, bringing all data under one roof. This helps to identify and address issues, giving real-time feedback on product performance. Manufacturing companies can then pinpoint areas for improvement and ensure they’re more prepared when market changes occur.
Through strategic planning and preparation for the move to DX, manufacturers can achieve high standards of operational excellence. Once the use cases have been assessed, companies must outline specific goals and strategies.
Selecting a trusted partner to begin your DX journey with ensures impactful results, providing a competitive edge in the market. For further insights into maximising the benefits of DX, explore our 5 steps to identifying its value.