Years ago, when parametric technology and features first came about, it’s not an exaggeration to say that it revolutionised the CAD industry. This technology really changed the way that engineering organisations not only developed 3D models, it also changed the way that they made amends to the drawings as well. Even recently, research has shown the benefits of building intelligence into models and modular approaches that really provide a lot of power and help automate a lot of the engineering process.
What are the advantages of parametric modeling?
Parametric modeling brings engineers many advantages. For instance, once you have made a part that will be used in many models, then the part can be archived so that in the future it can be recalled rather than remodeled. And, because it is possible to embed intelligence with a design, it allows engineers to pass this design intelligence to other engineers throughout the lifecycle of the product.
With a parametric approach, it is possible to add constraints to parts, meaning that they cannot be altered by mistake later on in the design process. In other words, constraints are a way of ensuring that any modifications made to the design are done so with design intent in mind.
What are the limitations of parametric modeling?
But, it hasn’t all been positive. The way that these constraints work is that they often have references that can work against each other. While this can empower a lot of intelligence in a design and in a model, it can also prove to be restrictive. For instance, a change to a feature very early on in the model can have a dramatic effect on the subsequent features. Sometime the unintended effects can even cause a model to fail.
There is a real challenge here. Sometimes, you follow some very strict rules and paths, where the restrictions work well. But, other times you want to freedom to explore design options more freely. This is where the restrictions can be limiting. These constraints can slow down the innovation process and even force engineers to have to recreate parts of a model because of a failure.
Can engineers overcome these limitations?
In recent years, there have been big changes that have helped this situation. The emergence of direct modeling as another effective way to create 3D models offers engineers more flexibility. There have also been improvements in sketching and 2D tools. As well, there are tools like Creo Flexible Modeling, which now allow you to make changes directly into a parametric model, without being limited by the constraints. With Creo Flexible Modeling, it is simple to choose and modify the full range of your design geometry, including rounds and patterns. On top of this, the full design intent is maintained.
Find out more about modern CAD tool and get your free trial of Creo Parametric today
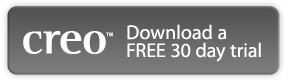